|  |
Parts list
- 45 gallon drum (55 gallons US)
- 4x4ft 1-1/2x1-1/2" steel angle
- 2x 2ft approx. 1-1/2x1-1/2" steel angle
- Shaft approx. 1" 4ft long
- 2x Bearings to fit shaft with grub screws
- Pulleys to give 2:1 reduction
- Motor running at 1500rpm
- Stirring blade
- Copper pipe
- Various plumbing fittings
- Drain tap(s)
The shaft could possibly come from a lawn mower or a go-kart.
For the bearings I used one pillow block and one flange type -- it would have been two pillow blocks but I cracked the housing getting the second one off the shaft it was on.
For the stirring blade I used a cooling fan blade from an Austin A35. The first test with water proved this to be too big -- the water flew all over the place. I cut it down to about 5". It's welded to an old gear that fits the shaft.
Building the mixer
Start with a 45 gallon drum. Cut half the top out using a hammer and chisel. Cut the two 2ft lengths of 1-1/2x1-1/2" angle so as they fit inside the drum. Make them the same length and the bearings will line up. Mark out and drill the angle to take the bearings. Weld one piece of angle under the top and onto the side. Weld the other about 8" from the bottom.
The bottom angle welded in place, with the bearing fitted and the shaft in place. This is the mixer blade before it was cut down. A piece of steel about 5"x1" could be welded into a slot cut in the end of the shaft instead. |
 |
Heating element made from copper pipe. This is heated from a tank of hot water in the workshop. It could be connected to the central heating. |
 |
Motor and pulley fitted -- the blade turns at about 800rpm.
Facing the camera on the right are the water inlet and outlet for the heating element; on the left of the processor are the two drain taps, one at the bottom, the other higher up. |
 |
From the other side, showing how the motor is fitted.
The four 4ft lengths of steel angle serve as legs and two of them also hold the mounting plate for the motor. |
 |
Detail showing how the motor is fitted to a plate mounted to two of the steel angle uprights. |
 |
The Austin cooling fan blade cut down to 5", which works well. |
 |
The heating element circulation pump installed.
Ready to go! |
Simon Wells is an engineer who lives in Reading, England. This is his Mark II biodiesel processor -- visit Simon's website for photographs and details of the smaller Mark I, now being used for mixing the sodium methoxide, which is then transferred to the big Mark II mixer via a solvent pump.
http://www.veggiepower.org.uk
Email: simon.wells2@btinternet.com


© Simon Wells 2000, 2001
Touchless processor
Dale Scroggins's processor is "a 100-liter processor made from mostly salvaged materials that almost fills itself, mixes everything, recovers the unused methanol, washes and dries the ester pretty much by flipping a few switches... I first evacuate the tank, then suck in the oil through a filter setup that I'm a little too proud of. I mix the methoxide separately, using a drill press with a paint mixer installed, then suck it into the tank. Then flip the pump switch. Watch through the clear hoses and marvel. Later, flip off the pump switch, check for separation, flip on the vacuum pump (which is connected to a liquid trap which is connected to the condenser which is connected to the tank) and watch the excess methanol collect in the trap. When no more collects, I open the tank to the atmosphere and drain off the glycerine. Then suck in water and begin the wash." (From a message to the Biofuel mailing list, 11 Jan 2001)
Full description, more photos and drawings
Closed loop processor
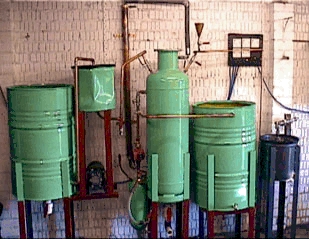
Ian Jackson's 80-litre per batch closed loop processor (experimental) |
Construction details:
http://www.veggiepower.org.uk/page301a.htm
Schematic:
http://www.veggiepower.org.uk/page302a.htm
Photo 1:
http://www.veggiepower.org.uk/page303a.htm
Photo 2:
http://www.veggiepower.org.uk/page304a.htm
Photo 3:
http://www.veggiepower.org.uk/page305a.htm
Make your own continuous reactor! Oscillatory Flow Mixing (OFM) provides highly effective mixing in tube reactors by the combination of fluid oscillations and baffle inserts ... OFM is particularly suited to continuous processing. How it works, Research, Technology, Publications, and more, with diagrams and photographs.
http://www.cheng.cam.ac.uk/groups/polymer/OFM_page.html
Biofuels at Journey to Forever
Biofuel
Biofuels Library
Biofuels supplies and suppliers
Biodiesel
Make your own biodiesel
Mike Pelly's recipe
Two-stage biodiesel process
FOOLPROOF biodiesel process
Building a biodiesel mixer
Biodiesel in Hong Kong
Nitrogen Oxide emissions
Glycerine
Biodiesel resources on the Web
Do diesels have a future?
Vegetable oil yields
Bubble washing
Biodiesel and your vehicle
Food or fuel?
Ethanol
Ethanol resources on the Web
Is ethanol energy-efficient?
|  | 
|